In The News
When to Automate?
Systems integrators like S&R Robot Systems help in determining how automation of packaging and palletizing will increase productivity and reduce operational expenses. As automation equipment becomes increasingly affordable, the amount of options in automating with robots increase. Asking the right questions are key in determining how robot automation can increase palletizing or case packing productivity. An article, written by Mike Aimone, published in September 2013 of Control Engineer outlines six steps for determining when to automate. A few of these steps listed in the article are:
1. Start with a pie-in-the-sky list.
2. Find the how (Call S&R Robot Systems)
3. Prove It (Justification)
etc..
For more information on this article and the remaining steps, pick on the link below:
S&R Robot Systems is a system integrator for Kuka robotics and Motoman robotics, located in Plano Texas.
S&R Robot Systems has Moved
It is an exciting day for S&R Robot Systems. We have moved to a larger building in Plano, Texas. This move to Plano allows S&R to integrate larger robot palletizing systems including larger robots. In addition, Plano offers better area attractions for hosting S&R customers. In the near future, we will be hosting an open house. Until that time, please feel free to stop by and check out our new home.
Our new address is now:
S&R Robot Systems LLC
1401 Summit Avenue
Suite 1
Plano, TX 75074
Is Your Goal to Improve Operations, How About a Robot Palletizing System?
Eliyahu Goldraratt in his book, The Goal, stated “Productivity is meaningless unless you know your Goal.” Most companies seeking a robot palletizing system have as their primary goal to reduce operating costs. Reducing operational costs combined with increasing flexibility, balancing production line throughput, or increasing personnel safety will help a company become more competitive. Robot integrators like S&R Robot Systems located in Texas can assists how a robot palletizing system can help improve goals such as these.
Flexibility is a strategic advantage with robot palletizing systems. Companies manufacturing various products on a single line or packaging in various containers can automate this process with a robot system. End of arm tools (EOAT) are custom-designed to handle a wide range of products, from boxes and bags, cartons and cases, to pails and pouches, kegs and barrels. An EOAT can be swapped automatically, allowing a single robot to palletize 50lb bags and 55 gallon drums virtually seamlessly.
Not only can a robot palletizing system palletize various product types, but it’s flexible enough to expand with a growing company that is continually adding new products. Growing companies must be able to quickly expand or retool for new products. Retooling a robot palletizing system can be as easy as programming new stack patterns on a pallet. In addition, a robot can be redeployed to operations other than palletizing. If production can benefit with manufacturing flexibility, then a robot system is a good solution.
A balanced, high performance production line has little or no bottle necks with throughput. Many companies have to contend with business cycles and finding a balance with regard to manual labor; needing to hire new employees or contractors when sales are above capacity and faced with lay-offs when sales are down. A robot palletizing system helps balance labor challenges in dealing with business cycles. Also, companies faced with production backlogs or shortages tend to balance this challenge by increasing inventory. Automating with a robot palletizing system helps balance a production line and thus, assists with reducing inventory.
Any company that manufactures heavy, bulky items or smaller high-volumes products with multiple shifts will benefit by implementing a robot palletizing system. The manual process of handling products greater than 50 pounds, palletizing at fast rates for long periods, or stacking product above the head leaves opportunity for personal injury. For extremely heavy products, robot suppliers like Kuka Robotics provides palletizing robots capable of payloads up to 2000lbs. Some products are manufactured in extreme environments where exposure to injury is high, like metal stamping and forging operations. A robot system can mitigate these risks, as well as others that may be specific to your operation.
Reducing operational cost may be the ultimate goal; however, the true benefit with a robot system is improving multiple measures at one time. When considering a robot system, companies should evaluate reducing operation expenses and increasing manufacturing flexibility and increasing throughput with a balanced production system. Companies with high-volume production, bulky/heavy products, multi-product handling needs, unbalance production lines, and needing increased focus on safety should consider the benefits of a robot palletizing system.
Contact us today at 972-271-5203, x30, or sales@robotsystemsllc.com for a free automation assessment, and let us show you the advantages that a robot palletizing system can provide for you.
About the Author: Jason Reagan is General Manager and Co-Founder of S&R Robot Systems. To learn more about the people at S&R Robot Systems please visit our web site at: http://www.robotsystemsllc.com/s-r-advantages/the-team/
Advantages of a Robot Palletizing System
Any company that manufactures a product, especially large, heavy items packaged in boxes or bags, and places those items on a shipping pallet, is a candidate for automated palletizing equipment, and there are several choices in the type of equipment these companies can consider. Since automation has made great strides in recent years, one of the top choices today is a robot system because it offers more features and benefits than other palletizing equipment.
According to experts in this specialized equipment area, robots offer many benefits over conventional palletizers. Robots:
- need less overall space for complete operation
- can handle heavy loads
- can handle multiple production lines
- provide the flexibility to handle various stack patterns
- offer fully-automated end of arm tool (EOAT) change-over to handle multiple products
- can adapt to new product extension and/or change-over more easily and cost-effectively than dedicated palletizing equipment
- can multi-task in the production process to provide case-packing, pallet loading and potentially others tasks in addition to palletizing
As with most other industries, reducing personnel costs to compete in today’s global economy is a top priority for manufacturers. The current focus on continuous improvement requires that all aspects of today’s manufacturing processes be scrutinized to maximize efficiency wherever possible. And, while most manufacturing companies have made significant investment in automating the front end of their production process, many have neglected to update their packaging and palletizing processes, which remain time and labor intensive.
When considering the safety that robots offer when compared to a person stacking and lifting, the overall savings can be even more significant. The benefits are multiplied:
- Fewer labor hours
- Fewer claims for workmen’s compensation
- Damaged products are generally reduced
- Errors are reduced
- Returns are reduced
- Shipping costs on both ends go down
- Overall product cost is reduced
S&R Robot Systems takes all these factors into account when designing your robot palletizing system. Since we have been building complex control systems for over a decade, we are able to not only see the bigger framework of your packaging needs, but we know where the problems are likely to arise, and we will mitigate the likelihood of those problems. With consulting, project management, design, implementation and monitoring all part of our expertise, S&R can develop palletizing solutions for virtually any industry.
Contact us today at 972-271-5203, x30, or sales@robotsystemsllc.com for a free automation assessment, and let us show you the advantages that a robot palletizing system can provide for you.
Robots Sales Continue to Boom in North America
North American businesses continue to lower production cost by implementing robot systems. The robot industry has enjoyed a year of strong sales, according to Controldesign.com:
“Robotics companies based in North America are enjoying another strong year, with new orders up 20%, according to the Robotic Industries Assn. (RIA). An estimated 225,000 robots are used in factories here; the U.S. is second only to Japan in robot use. It’s still only the tip of the iceberg in market potential, however.
North American companies ordered 16,363 robots valued at more than $1 billion in the first nine months, a unit increase of 20% and value increase of 29% compared with the same period in 2011.“
…
“The robotics market shows significant room for growth, Burnstein indicated. “Many observers believe that only about 10% of the U.S. companies that could benefit from robots have installed any so far,” he said. “Among those that have the most to gain from robots are small and medium-sized companies.”
Controldesign.com | “North American Robotics Continues to Boom”
http://www.controldesign.com/industrynews/2012/north-american-robotics-continue-to-boom.html
The growing robot automation market is an indication that robot systems are a means to becoming more competitive. S&R Robot Systems provides free assessment to help its customers determine the benefits on implementing robot systems.
Dallas, TX Local Robot Integrator
Dallas, TX is host to a number of great opportunities, including Texas State Fair corn dogs, Cowboys at the Fort Worth Stock Yards, and an integrator for automated robot systems. S&R Robot Systems LLC would like to welcome you to the release of our new website. Please take a seat and feel free to look around at the products and service that we have to offer. If you have any question, please contact us at info@robotsystemsllc.com.
How Robots Can Help Your Manufacturing Business
Growing popularity has made robotic solutions an affordable option for small businesses
Manufacturing often includes repetitive, simple jobs that can be quickly and efficiently performed by machines. While it may seem like something out of “The Jetsons,” there are robotic machines, a.k.a robots, that can help your small business by executing recurring tasks, such as applying liquid coatings or moving objects around factories. These machines can also protect against injury by handling dangerous assignments, like cutting or welding metals.
Many small manufacturers assume that robots are out of their price range. But robots have become increasingly affordable as they’ve grown more prevalent. Several companies, such as RobotWorx, even specialize in economical used or refurbished units that can make robots affordable for your business. While robots can reduce labor costs and increase production speed, there are also some pitfalls:
- Robots need regular maintenance. Most robot manufacturers offer maintenance training and service plans for an added fee.
- Software to run your robots is usually included, but some companies make you buy software from outside sources.
- Look for a robotics company that offers a simulation to demonstrate how your robot would operate. This helps you and the robot manufacturer foresee potential issues, so that they can be addressed before the robot goes to production.
- Account for the additional amount spent on electricity; robots can cause your bill to jump more than you realize.
Small-business owners can get referrals from engineering consultants and manufacturers who specialize in automated robotics. The Robotics Industries Association is a good source for the latest industry news, a buyer’s guide and robotics company listings.
What do you want your robot to do? Robotic assembly equipment can be customized to meet your needs, but standard designs are also available. Whether or not your manufacturing process requires custom machinery depends on what function you need your robots to perform and the complexity of your manufacturing process.
Robot breeds include these:
Dispensers can perform a multitude of routine tasks to free up your human employees for jobs that require more thought. They can reliably and efficiently apply adhesives or sealants, recognize bar codes and pull specific items from your stockroom, or unload parts.
These robots are essentially oversized dispensers, handling heavy and cumbersome pallets. Robotic assembly palletizers can unload products from conveyor belts and assembly lines and group them for shipping and processing. Palletizers can also be used to package products or unload incoming shipments. If you’re considering a palletizer, make sure yours could handle the weight required by your process, as maximum capacity varies by design.
For advanced projects, robotic assembly arms can conduct dangerous or difficult tasks. These machines can be programmed to remove products from molds, X-ray parts, or use a laser to cut through tough surfaces. While these may seem more advanced, welding robots are among the most commonly used by small businesses, and are easy to install and operate. Robotic assembly arms require periodic recalibration or reprogramming to maintain their precision, however, which increases the cost.
Custom robots can be engineered to meet your manufacturing needs if you need them to handle atypical or advanced functions. Customization is also necessary when a robot is expected to work in extreme conditions, such as a sterile or extremely cold environment. Made-to-order machines are more expensive, of course, but they are especially tailored to your specifications.
Brian Luskey is an associate editor at Business.com, the web’s largest business-to-business searchable directory and home to more than 35,000 business how-to guides.
Robots speak simpler programming languages
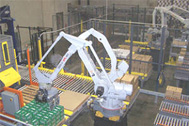
Robotics programmers can now use PAC platforms and languages they already know when deploying robots in material-handling applications.
Erik Nieves, technology director, Yaskawa Motoman Robotics
02/15/2011
Consumer-goods and food-production companies employ controls experts trained to manage complex factory-communications networks. As these companies seek wider adoption of robotics within picking, packing, and palletizing (3P)—at the expense of hard-automation lines-robots must be able to communicate easily and effectively within existing networks.
Allowing robots to take their commands from a programmable automation controller (PAC) rather than their own unique and proprietary control platform would allow robots in 3P applications to be embedded in the manufacturing controls rather than integrated to the controls.
For process-specific robotic applications, such as welding or painting, we want standard robots with their own proprietary controls and application-specific software. They exist in a larger manufacturing context and are integrated with control networks, but do their own thing for the most part. The controller firmware contains a wealth of process-specific information—for example, algorithms designed to optimize the arc-welding process to ensure smooth arc starts and minimize spatter. Internal control also keeps more processing overhead from being loaded onto the larger system.
Robots designed for these applications can be purchased with much of this process-specific programming built in, or chosen from libraries of applications. This helps get up and running faster, but such specialized programming is something of a black box to most engineers in the field who have not had specific training. They have little opportunity to understand what’s happening under the covers, but in most cases with those types of applications that isn’t really a problem.
In the consumer-goods and food-processing markets, most robots work in material-handling tasks such as assembly, packaging, and palletizing. Here, the integration process of marrying the robot controller to the rest of the workcell creates challenges and adds cost and time to the startup process.
In a recent announcement, Robotic Industries Association president Jeff Burnstein said he expects continued growth in the material-handling sector. “Material handling is important to just about every industry, and robots are reaching new users all the time,” he said.
The teams charged with installing, integrating, and managing these robots on a daily basis must have a great deal of robotics expertise. That is not a typical skill set often found in consumer-goods and food-processing plants. If the engineer overseeing the workcell does not have sufficient robotic experience, it can be difficult to optimize the installation in the context of the larger manufacturing line, and the ultimate result may never be entirely satisfactory.
For robot manufacturers to tap into that vast and growing material-handling arena, robot OEMs have two choices: Train more robot experts for these new markets, or recognize that industry is already flush with well-trained PAC experts, and leverage that knowledge base and develop technology that allows PAC/PLC experts to program and manage our robots.
Mixing it up: Trends in Packaging and Palletizing Robotics
Mixing it up: Trends in Packaging and Palletizing Robotics
by Bennett Brumson , Contributing Editor
Robotic Industries Association Posted 07/23/2008
The accelerating adoption of robotics has been among the most important trends in packaging and palletizing in recent years. With the speeds and flexibility that robotics offer, this trend will continue.
“Packaging and palletizing robotic applications are a growing industry. Just about everyone palletizes or packages their product,” says Kawasaki’s Bob Rochelle.
“The cost of robotic technology has come down while performance and user-friendliness continues to improve in packaging and palletizing applications,” says Dick Motley, Account Manager for Distribution Network with FANUC Robotics America Inc., Rochester Hills, Michigan. “The trend towards the widespread adoption of robotics in packaging and palletizing applications is similar to what we have seen in the computer industry.”
Packaging Trends
“Recent trends in packaging applications have seen an acceleration in the use of robotics over hard automation,” says John Dulchinos, President and Chief Operating Officer, at Adept Technology Inc., Livermore, California. “I see a couple of high-level trends that will continue in the next several years.”
The first trend Dulchinos speaks of is the movement away from general-purpose robots towards robots designed with packaging applications in mind. “The trend towards application-specific robots is due to the combination of high speeds and relatively low payloads necessary in packaging applications. Robots for packaging applications deliver speeds and performance beyond what traditional articulated or SCARA robots can deliver,” Dulchinos says. Higher speeds are fundamentally compelling for increased throughput per square foot for each robot in a manufacturing facility, he maintains.
Dulchinos’ second trend is the role of vision systems in packaging work cells. “Vision is more highly integrated in packaging robots because randomly oriented product placement at high speeds requires vision and conveyor tracking. In addition, color vision is replacing gray scale.” Dulchinos also says vision can be taught to recognize products that vary in shape, such as many food products.
As for the packaging itself, robots are handling more blister packages, those pre-formed plastic wrappers used for packaging everything from small consumer goods to unit-dose packaging of pharmaceuticals. “The biggest trend I see is more blister packs,” observes JR Musselman, Software Engineering Manager at Doerfer Companies, Greenville, South Carolina. “End-users like blister packs because they are inexpensive and can be handled at very high speeds.”
Robots are often called on to package irregularly shaped items. Robert Rochelle, North America Sales Manager with Kawasaki Robotics (USA) Inc., Wixom, Michigan, describes such a project. “If a box is going to be stuffed with something irregularly shaped, like a lawn mower, we take data of its smallest to largest dimensions. We design the tooling and the pallet pattern to take into account the largest dimension.” Rochelle points out that by doing a little reverse engineering, work cells are integrated to get the result the end-user needs.
Bigger Pallets, Smaller Pallets
Robotic palletizing also has picked up a great deal in the last several years, according to Richard Tallian, Robotic Consumer Industry Segment Manager, ABB Inc., Auburn Hills, Michigan. “We are seeing a trend away from traditional palletizing work cells where a robot services up to four product in-feed stations and up to four outgoing pallets,” Tallian says. “The robotics industry is now seeing projects where a single robot is dedicated to a single end-of-line palletizing station. End-users are trying to avoid conventional material handling equipment.” Instead, end-users are putting robots at the end of the line to do complete palletizing operations, submits Tallian.
Tallian adds that larger end-users are driving a change towards smaller pallets that are used as displays in their stores. These pallets are assembled in a warehouse, trucked to the point of retail and put directly into stores. “Large retail stores are moving away from conventional pallets, which were traditionally loaded to heights over 86 inches. Now we are seeing more pallets loaded to 56 inches because the end-user wants these pallets placed directly into a store as end-of-aisle displays.”
Likewise, Dick Motley of FANUC Robotics says large retailers are having an impact on robotic palletizing, saying, “Large distribution channels impose specific requirements on packaging and palletizing configurations, which demand versatility from the application. This has lead to a significant ramping up of packaging and palletizing robotics in the last few years and an acceleration of (the number of) manufacturers who purchase robots for packaging or palletizing applications.”
On the other end of the size scale, some end-users want robots to build larger pallets to maximize trucking efficiency. “The trend has been towards 110-inch high pallets, because that is what end-users can transport with by truck,” observes Brian Kocks, Sales Manager for Modules and Robotics, with Güdel Inc., Ann Arbor, Michigan. Loads are also getting heavier. “We are starting to see payloads going over the standard 100 kg.”
Dual-arm robots will become more commonplace in the coming years, predicts Tom Sipple, Handling Technology Leader at Motoman Inc., West Carrollton, Ohio. “Two arms allow for simultaneous operations, and facilitate handling of unwieldy objects like cases, trays or divider sheets. End-of-arm-tools can be simpler on dual-arm robots, which helps avoid interference and could allow for more flexible designs,” Sipple contends.